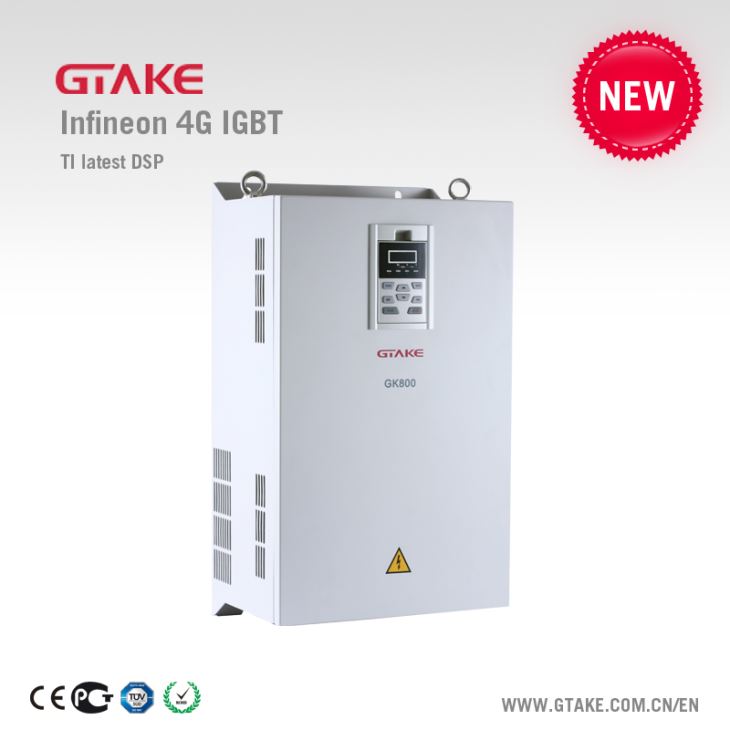


GK800-4T355 Variable Speed Drives
-
Payment
-
Origin
China Mainland
-
Minimum Order
15
-
Packing
Pieces
- Contact Now Start Order
- Description
Product Detail
GK800 Closed-loop Vector Control Variable Speed Drive
GK800 Series High Performance Variable Speed Drives, adopting most advanced close-loop vector control technology, are able to perform precise control on both asynchronous motors and permanent magnet synchronous motors. GK800 series, one of the real drives leaders, are superb in demanding applications with excellent performance no matter in speed control, torque control, position control, field weakening control, or response time, and so on.
GK800 supports position control, with expansion boards of EPC-PG1 and EPC-PG2 available. For detailed instructions of the expansion boards, please email me or download from our website.
EPC-PG1: Support open collect, and push-pull encoder signal input, with power supply 12V. Support A/B/Z signal open collector frequency dividing output (applicable for asynchronous motor only)
EPC-PG2: Support open collector, push-pull, and differential encoder signal input, with power supply 5V/12V programmable. Support A/B/Z signal frequency dividing output, i.e. A+/A-, B+/B-, Z+/Z- (applicable for asynchronous motor only)
For position control, please see the parameters below: For details, please refer to GK800 user manual.
Group F4 Position Control | ||||
F4-00 | Position Control Mode | 0: Non-position control | 0 | × |
F4-01 | Positioning completed width | 0~3000 | 10 | × |
F4-02 | Positioning completed time | 0.000s~40.000s | 0.200s | × |
F4-03 | Position loop gain | 0.000~40.000 | 1.000 | ? |
F4-04 | Zero-servo starting frequency | 0.00Hz~upper limit frequency | 1.00Hz | × |
F4-05 | Motor spindle orientational position 1 | 0~[4×(d6-07)-1] | 0 | ? |
F4-06 | Motor spindle orientational position 2 | 0~[4×(d6-07)-1] | 0 | ? |
F4-07 | Motor spindle orientational position 3 | 0~[4×(d6-07)-1] | 0 | ? |
F4-08 | Motor spindle orientational position 4 | 0~[4×(d6-07)-1] | 0 | ? |
F4-09 | Motor spindle orientation direction | 0: Orientation from current rotating direction | 0 | × |
F4-10 | Motor spindle orientation speed | 0.00Hz~upper limit frequency | 10.00Hz | × |
F4-11 | Motor spindle orientation decel time | 0.0s~60.0s | 2.0s | × |
F4-12 | Orientation position confirmation time | 0.000s~6.000s | 0.010s | × |
F4-13 | Return to origin option | 0: Disabled | 0 | × |
F4-14 | Return-to-origin direction | 0: Forward return-to-origin | 0 | × |
F4-15 | Return-to-origin frequency 1 | 0.00Hz~upper limit frequency | 10.00Hz | × |
F4-16 | Return-to-origin frequency 2 | 0.00Hz~10.00Hz | 1.00Hz | × |
F4-17 | High bits of feed 0 | 0~9999 | 0 | ? |
F4-18 | Low bits of feed 0 | 0~9999 | 0 | ? |
F4-19 | High bits of feed 1 | 0~9999 | 0 | ? |
F4-20 | Low bits of feed 1 | 0~9999 | 0 | ? |
F4-21 | High bits of feed 2 | 0~9999 | 0 | ? |
F4-22 | Low bits of feed 2 | 0~9999 | 0 | ? |
F4-23 | High bits of feed 3 | 0~9999 | 0 | ? |
F4-24 | Low bits of feed 3 | 0~9999 | 0 | ? |
F4-25 | High bits of feed 4 | 0~9999 | 0 | ? |
F4-26 | Low bits of feed 4 | 0~9999 | 0 | ? |
F4-27 | High bits of feed 5 | 0~9999 | 0 | ? |
F4-28 | Low bits of feed 5 | 0~9999 | 0 | ? |
F4-29 | High bits of feed 6 | 0~9999 | 0 | ? |
F4-30 | Low bits of feed 6 | 0~9999 | 0 | ? |
F4-31 | High bits of feed 7 | 0~9999 | 0 | ? |
F4-32 | Low bits of feed 7 | 0~9999 | 0 | ? |
F4-33 | Position setting mode | 0: X7/DI pulse input + terminal direction input | 0 | × |
F4-34 | Numerator of electronic gear ratio | 1~9999 | 1000 | × |
F4-35 | Denominator of electronic gear ratio | 1~9999 | 1000 | × |
F4-36 | Feed-forward gain | 0.000~7.000 | 1.000 | ? |
F4-37 | Feed-forward filtering time | 0.000s~7.000s | 0.001s | ? |
F4-38 | Position offset change rate | 0~9999 | 800 | × |
1. Distinctive advantages of GTAKE close-loop vector control Variable Speed Drive
Based on the top software and hardware elite, modern and scientific producing workmanship, rigorous quality control systems and management team, GTAKE Frequency Inverters have many advantages, some of which are listed as below:
• Apply to asynchronous AC motor and permanent magnet synchronous AC motor;
• Starting torque:180% at 0.25Hz (SVC pattern), 200% at 0Hz (VC pattern);
• Speed adjustable range: 1:200 (SVC pattern), 1:1000 (VC pattern);
• Speed accuracy: +/-0.2% (SVC pattern), +/-0.02% (VC pattern);
• Over load capability: 150% 1minute, 180% 10s, 200% 0.5s;
• Abundant frequency command sources;
• Diverse input and output terminals;
• Ambient temperature: -10°C~50°C;
• High precise torque constraint, process PID control, simple PLC, wobble frequency control, contracting brake control, field weakening control, all sides protection, etc.
• Online and offline autotune of motor parameters can both performed;
• Extremely short-time acceleration can be performed without any trip, such as 0.1s or 0s from 0Hz to 50Hz;
• No derating ambient temperature: -10-50 centigrade;
• Customized products and services are also welcome;
• Flexible command sources, parameters setting, and all sided equipment protection function automatically;
• The malfunction ratio is lower than 1% within warranty period, based on the statistics.
2. Wiring Diagram of GK800 High Performance AC Drives
3.Information of Product Model
Technical Features of GK800 series Motor Frequency Inverters
3AC 380V/400V/415V/440V/460V/480V -10%~10%, 50Hz/60Hz -5%~5%
Model | Power Rating (kW) | Rated Output Current (A) | Rated Input current (A) | Applicable motor (kW) | Brake unit |
GK800-4T2.2B | 2.2 | 5.5 | 9.2 | 2.2 | Built-in |
GK800-4T3.7B | 3.7 | 9 | 14.9 | 3.7 | |
GK800-4T5.5B | 5.5 | 13 | 21.5 | 5.5 | |
GK800-4T7.5B | 7.5 | 17 | 27.9 | 7.5 | |
GK800-4T11B | 11 | 24 | 39 | 11 | |
GK800-4T15B | 15 | 30 | 50.3 | 15 | |
GK800-4T18.5(B)* | 18.5 | 39 | 60 | 18.5 | Built-in optional |
GK800-4T22(B)* | 22 | 45 | 69.3 | 22 | |
GK800-4T30(B)* | 30 | 60 | 86 | 30 | |
GK800-4T37(B)* | 37 | 75 | 104 | 37 | |
GK800-4T45(B)* | 45 | 91 | 124 | 45 | |
GK800-4T55 | 55 | 112 | 150 | 55 | Externally mounted when needed |
GK800-4T75 | 75 | 150 | 201 | 75 | |
GK800-4T90 | 90 | 176 | 160** | 90 | |
GK800-4T110 | 110 | 210 | 192** | 110 | |
GK800-4T132 | 132 | 253 | 232** | 132 | |
GK800-4T160 | 160 | 310 | 285** | 160 | |
GK800-4T185 | 185 | 350 | 326** | 185 | |
GK800-4T200 | 200 | 380 | 354** | 200 | |
GK800-4T220 | 220 | 430 | 403** | 220 | |
GK800-4T250 | 250 | 470 | 441** | 250 | |
GK800-4T280 | 280 | 520 | 489** | 280 | |
GK800-4T315 | 315 | 590 | 571** | 315 | |
GK800-4T355 | 355 | 650 | 624** | 355 | |
GK800-4T400 | 400 | 725 | 699** | 400 |
** means GK800-4T110 or above is provided with an external-mounted DC reactor in shipment as default
1AC/3AC 208V/220V/230V 50/60Hz -10%~10%, 50Hz/60Hz -5%~5%
Model | Power Rating (kW) | Rated Output Current (A) | Applicable motor (kW) | Brake unit |
GK800-2T2.2B | 2.2 | 10 | 2.2 | Built-in |
GK800-2T3.7B | 3.7 | 16.5 | 3.7 | |
GK800-2T5.5B | 5.5 | 24 | 5.5 | |
GK800-2T7.5B | 7.5 | 30 | 7.5 | |
GK800-2T11(B) | 11 | 45 | 11 | Built-in optional |
GK800-2T15(B) | 15 | 60 | 15 | |
GK800-2T18.5(B) | 18.5 | 73 | 18.5 | |
GK800-2T22(B) | 22 | 96 | 22 | |
GK800-2T30 | 30 | 112 | 30 | Externally mounted when needed |
GK800-2T37 | 37 | 144 | 37 | |
GK800-2T45 | 45 | 176 | 45 | |
GK800-2T55 | 55 | 210 | 55 | |
GK800-2T75 | 75 | 288 | 75 | |
GK800-2T90 | 90 | 310(350) | 90 | |
GK800-2T110 | 110 | 415 | 110 |
4. Technical features of GK800 Variable Speed Drive
Table 3 Technical features of GK800 Variable Speed Drive
Power input | Rated input voltage | 3-phase AC208V/220V/230V/240V/380V/400V/415V/440V/460V/480V |
Rated input current | See Section 2.3 in the User Manual | |
Frequency | 50Hz/60Hz, tolerance ±5% | |
Allowable range of voltage | Continuous voltage fluctuation ±10%, short fluctuation -15%~+10%, i.e. 323V~528V; | |
Voltage out-of-balance rate <3%, distortion rate as per the requirements of IEC61800-2 | ||
Power output | Applicable motor(kW) | See Section 2.3 in the User Manual |
Rated current(A) | See Section 2.3 in the User Manual | |
Output voltage(V) | 3-phase: 0~rated input voltage, error < ±3% | |
Output frequency(Hz) | 0.00~ 600.00Hz;unit: 0.01Hz | |
Overload capacity | 150% - 1min;180% - 10s; 200% - 0.5s | |
Control characteristics | V/f patterns | V/f control |
Sensor-less vector control 1 | ||
Sensor-less vector control 2 | ||
Close-loop vector control (including position control) | ||
Speed range | 1:100 (V/f control, sensor-less vector control 1) | |
1:200(sensor-less vector control 2) | ||
1:1000(close-loop vector control) | ||
Speed accuracy | ±0.5% (V/f control) | |
±0.2%(sensor-less vector control 1 & 2) | ||
±0.02%(close-loop vector control) | ||
Speed fluctuation | ±0.3%(sensor-less vector control 1 & 2) | |
±0.1%(close-loop vector control) | ||
Torque response | < 10ms(sensor-less vector control 1 & 2) | |
< 5ms(close-loop vector control) | ||
Torque control accuracy | ±7.5%(sensor-less vector control 2) | |
±5% (close-loop vector control) | ||
Starting torque | 0.5Hz: 180% (V/f control, sensor-less vector control 1) | |
0.25Hz: 180%(sensor-less vector control 2) | ||
0Hz: 200% (close-loop vector control) | ||
Positioning accuracy | ±1 line pulse | |
Basic functions | Start frequency | 0.00~ 600.00Hz |
Accel/Decel time | 0.00~60000s | |
Carrier frequency | 0.7kHz~16kHz | |
Frequency command sources | Digital setting + keypad ?/? | |
Digital setting + terminal UP/DOWN | ||
Communication | ||
Analog setting(AI1/AI2/AI3) | ||
Terminal pulse setting | ||
Motor started methods | Started from starting frequency | |
DC brake then started | ||
Speed search started | ||
Motor stopped methods | Ramp to stop | |
Coast to stop | ||
Ramp to stop + DC brake | ||
Basic functions | Dynamic brake capacity | Brake unit threshold voltage: 650V~750V; service time: 0.0~100.0s; brake units of GK800-4T45 and below are built in or can be built in. See table 2-1 |
DC brake capacity | DC brake start frequency: 0.00~600.00Hz | |
DC brake current: 0.0~100.0% | ||
DC brake time: 0.0~30.00s | ||
Input terminals | 7 digital inputs, one of which can be used for high-speed pulse input. Compatible with active open collectors NPN, PNP and dry contact input. | |
3 analog inputs, one of which supports voltage input only, and the other two are voltage/current programmable. | ||
Output terminals | One high-speed pulse output terminal, 0~50kHz square signal; can output command frequency, output frequency and so forth | |
One digital output terminal | ||
Two relay output terminals | ||
Two analog output terminal, voltage/current programmable; can output command frequency, output frequency and so forth | ||
Encoder signal terminal | Compatible with 5V/12V encoder | |
Compatible with different types of encoder signal input, such as open collector, push-pull and differential, etc. | ||
Featured functions | Parameter copy, parameter backup, common DC bus, free switchover between two motors' parameters, flexible parameter displayed & hidden, various master & auxiliary command and switchover, reliable speed search started, a variety of Accel/Decel curves programmable, automatic correction of analog, contracting brake control,16-step speed control programmable (2 steps support flexible frequency command), wobble frequency control, fixed length control, count function, three faults recorded, over excitation brake, over voltage stall protection programmable, under voltage stall protection programmable, restart upon power loss, skip frequency, frequency binding, four kinds of Accel/Decel time, motor thermal protection, flexible fan control, process PID control, simple PLC, multi-functional key programmable, droop control, asynchronous and synchronous motor parameter identification, field-weakening control, high-precision torque control, V/f separated control, torque control at sensor-less vector control, torque control at close-loop vector control, two encoder signal inputs (support incremental, UVW hybrid and resolver, etc.), flexible deceleration ratio control, zero servo, motor spindle orientation, simple feed forward control, pulse train position control | |
Protection function | Refer to Chapter 7 - Troubleshooting | |
Environment | Place of operation | Indoors, no direct sunlight, free from dust, corrosive gases, flammable gases, oil mist, water vapor, water drop and salt, etc. |
Altitude | 0~2000m | |
De-rate 1% for every 100m when the altitude is above 1000 meters | ||
Ambient temperature | -10?~50? | |
Relative humidity | 0~95%, no condensation | |
Vibration | Less than 5.9m/s2 (0.6g) | |
Storage temperature | -40?~+70? | |
Others | Efficiency at rated Amps | 7.5kW and below: =93% |
11~ 45kW: = 95% 55kW and above: =98% | ||
Installation | Wall-mounted | |
IP grade | IP20 | |
Cooling method | Fan cooled |
5. Environment requirement:
?Conditions: Indoors, free from direct sunlight, corrosive gases, flammable gases, oil mist, water vapor, metal particles, etc.
?Altitude: 0~2,000m. Derating is required above 1,000m, Rated output current should be derated 1% per 100m increase above 1000m.
?Ambient temperature: -10°C~50°C.Derating 1% per centigrade additional for temperature >50°C
?Vibration: Less than 5.9 m/s² (0.6g)
?Storage temperature: -40~70°C
?Protection grade: IP20
?Type of cooling: Air cooling
6. Applications:
Fan, oil pump, water pump, compressor, air compressor, injection molding machine, engraving machine, textile, packaging, conveyor, treadmill, printing machine, lathe, machine tool, hydraulic machine, wire drawing, winder/un-winder, knitting Machine, compressor, extruding machine, injection machine, AC motor, braiding machine, pressure fan, forced draught blower, blower, blowing machine, blow molding machine, root's blower, film blowing machine, cutter bar, cut-off machine, slitter, Cutting machine, grinder, cluster, glazing machine, polisher, polishing machine, laundry-drier, drying machine, ball crusher, ball grinding mill, drawing machine.
7. Key words
Frequency inverters, AC Drives, variable frequency drives (VFD), AC motor drives, frequency converters, frequency changers, adjustable speed drives (ASD), adjustable frequency drives (AFD), variable speed drives (VSD), AC motor speed controller, AC variable frequency drive, variable frequency inverter, AC motor speed controller, EMI filter, Input EMI Filters, Output EMI Filters, AC Choke, AC Reactor, Input AC Choke, Output AC Choke, Input AC Reactor, Output AC Reactor, DC Choke, DC Reactor, Input DC Choke, Output DC Reactor, Input DC Reactor, Servo Drive, Servo Motor & Drive, Servo Motor & Drive System
- GK800-4T132 Variable Speed AC Drives 15 Pieces / (Min. Order)
- GK800-4T200 AC Drives VFD 15 Pieces / (Min. Order)
- GK800-2T7.5B Big Starting Torque Variable Speed Drives 15 Pieces / (Min. Order)
- GK800-4T55 AC Variable Speed Drives 15 Pieces / (Min. Order)
- GK800-4T132 Variable Speed AC Drives 15 Pieces / (Min. Order)
- GK800-4T315 Variable Frequency Drive 15 Pieces / (Min. Order)
- GK800-2T45 VFD Drives 15 Pieces / (Min. Order)
- Variable Speed Drives For Fan 15 Pieces / (Min. Order)
- GK800-4T132 Variable Speed AC Drives 15 Pieces / (Min. Order)
- GK800-4T200 AC Drives VFD 15 Pieces / (Min. Order)
- GK800-2T7.5B Big Starting Torque Variable Speed Drives 15 Pieces / (Min. Order)
- Dedicated Frequency Inverter For Water Pump (GK600-48) 15 Pieces / (Min. Order)
- GK600-6T Series General Purpose AC Motor Drives 15 Pieces / (Min. Order)
- GK800-6T Series High Performance Vector Control VFDs 15 Pieces / (Min. Order)
- GK600-4T Series General Purpose AC Motor Drives 15 Pieces / (Min. Order)
- GK800-4T Series High Performance Vector Control VFDs 15 Pieces / (Min. Order)
- GK600-4T Series General Purpose AC Motor Drives 15 Pieces / (Min. Order)
- GK800-4T Series High Performance Vector Control VFDs 15 Pieces / (Min. Order)
- GK600-4T Series General Purpose AC Motor Drives 15 Pieces / (Min. Order)
- GK600-4T Series General Purpose AC Motor Drives 15 Pieces / (Min. Order)
- GK800-4T30(B) Big Starting Torque AC Servo Drives 15 Pieces / (Min. Order)
- GK800-4T132 Variable Speed AC Drives 15 Pieces / (Min. Order)